为把物流中心打造成为具有行业内一流管理水平的物流企业, 在2013年2月成立质量部开始试行实施“6S现场管理”。6S管理作为ISO9001标准的辅助方法,“6S现场管理”简单易行,从细节入手,由习惯到素养,提升基层员工的素质及安全作业能力,对美化厂区环境、硬件设施增值,效果立竿见影。
物流中心成立了以公司领导及业务骨干为主的6S管理推行小组,首先制定了符合本企业发展阶段的《6S管理试行计划书》、三易其稿制订了《物流中心员工6S管理试行考评办法》、《6S管理现场试行考评表》,下发了《储运部物资管理规定》、《各岗位6S操作指南》,做到规章制度与工作标准的公开化。
其次划分了各项目班组、员工的责任区域,制定了相关责任区域图及详细说明文件,明确责任,要求对所管理区域内发生的问题,责任人负责查找问题根源、提出合理方案及时改进。
为避免推行工作走入面子工程的误区,让员工误以为6S就是打扫卫生、罚款。鉴于多数员工对6S管理的了解似懂非懂,推行小组制定了逐步推进的管理方案,充分运用定点摄影手段,对违反6S标准的行为,拍摄成照片在6S宣传栏上曝光,在曝光的对比图片上标明违反6S的问题类别、错在哪里、改正的情况,通过典型对比图片让当事员工、其它员工都学会按正确的方法工作。
6S定点摄影案例:
案例1:整理-----托盘工装摆放
托盘的码放看似简单不重要,但与作业效率息息相关,例如未分类码放、不同品类进行混放,作业时为挑选合适托盘会浪费宝贵作业的时间,未按标准高度码放,数量须反复清点,作业时会多次低效作业消耗更多企业成本。

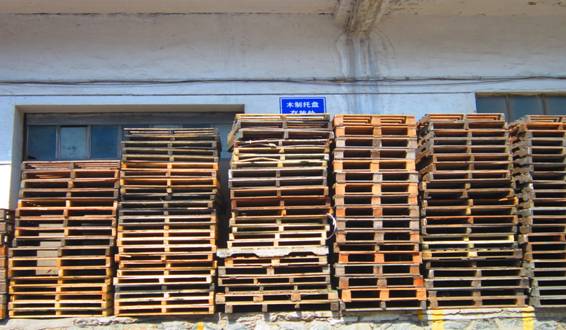

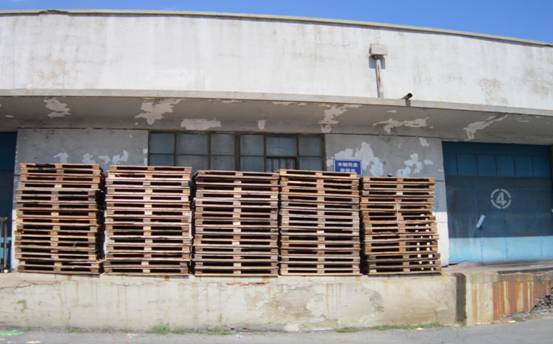
案例2:整理、整顿----叉车维修室管理
储运部叉车维修室叉车配件、工具未分类管理环境杂乱,并存在闲置物品未处理占用空间。改进后对工具和配件分类管理,无闲置物品充分利用空间。

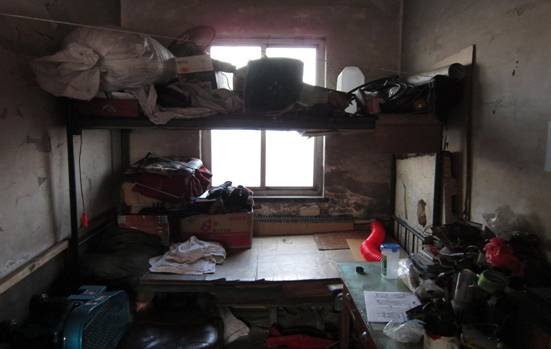

案例3:整理、整顿-----员工办公、休息区管理
原员工更衣室,随处可见闲置物品,个人物品不放在更衣箱内,办公区区域放置个人物品,严重影响物流中心形象。改进后储运部办公、休息区域无闲置物品,腾出员工休息、娱乐空间,外来人员休息空间,干净整洁的环境受到了客户的赞许。

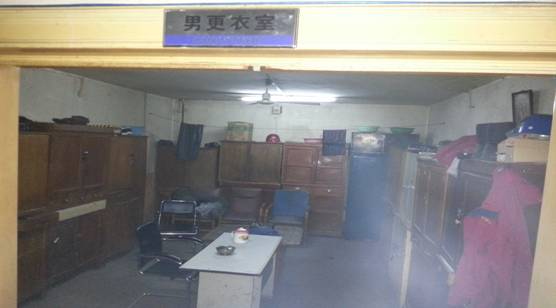

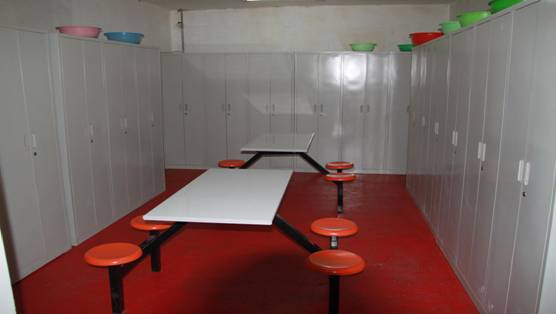
案例4:安全----物流作业安全
物流中心安全涉及库房、场地面积大,安全作业操作技术要求难度高,作业强度大。6S管理针对重点区域、设备,严格按公司制定安全作业制度规范每一个作业人员,通过提升员工安全意识和划分责任,作业相关人员保管员、吊车司机、装卸工,即互相监督又相互协作,以团队的力量来杜绝安全隐患。



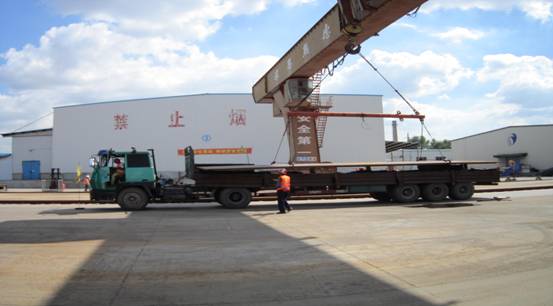

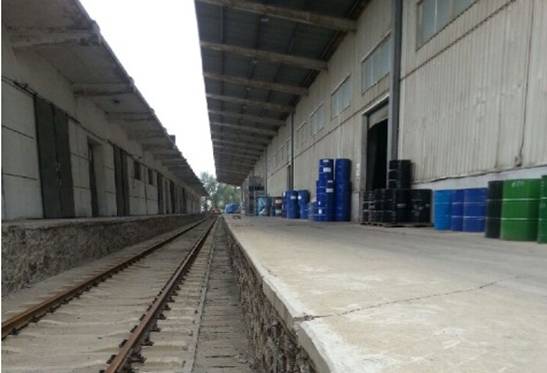

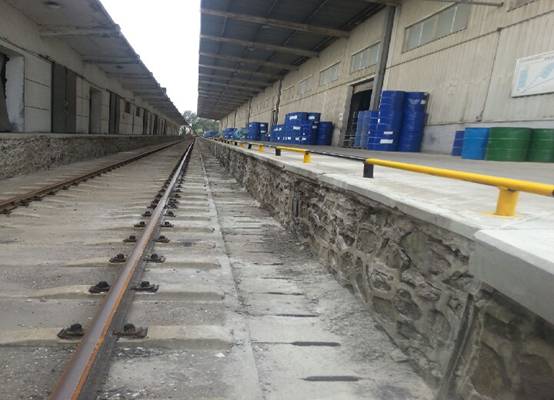

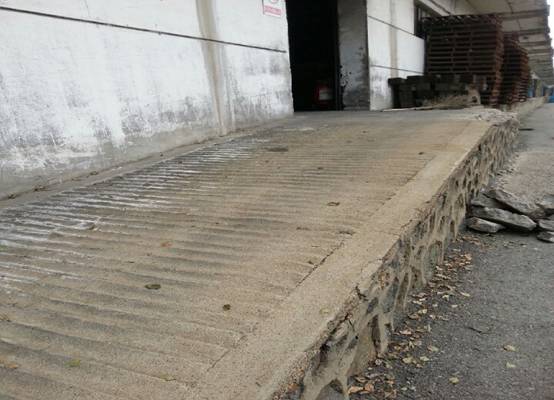

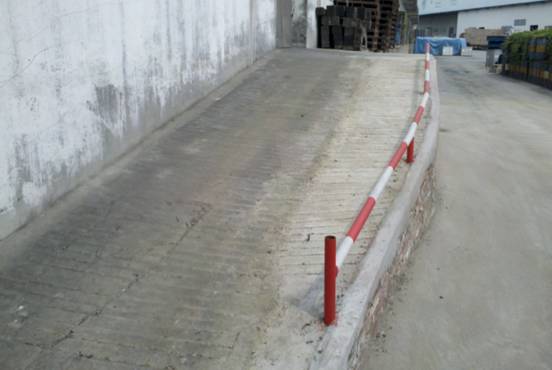
案例5:清洁----作业完毕后作业环境卫生清扫
作业完毕后作业环境卫生清洁问题,一直是物流中心整体卫生环境的根源之一,质量部通过对铁路到货作业垃圾、库房作业完毕未处理垃圾等问题的对比照片的曝光,找到问题根源。改进后保管员、叉车司机、装卸人员作业完毕后互相配合、互相监督清洁作业环境,谁作业谁负责。

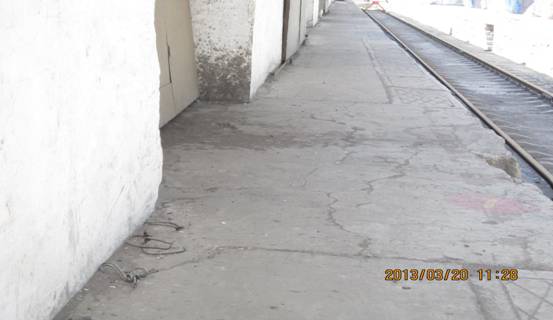

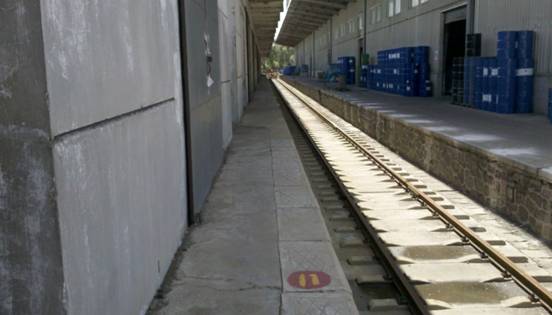
经过近6个月的试行“6S现场管理”,从标准规范化的物流作业,到劳保用品的佩戴,到作业前对设备的点检,对不安全行为的互相监督,员工素质正在发生质的改变。
高效的物流作业、干净整洁的库房场地环境,严格的安全管理措施,提升后的优质服务,带来了客户要求深化合作的商机,松下电池日方总经理亲自来物流中心考察后,要求设备课将新工厂进口设备装卸业务,交给物流中心来操作;2013年惠而浦主动要求续签项目合同,惠而浦给出了其所有第三方物流合同中最高的价格。
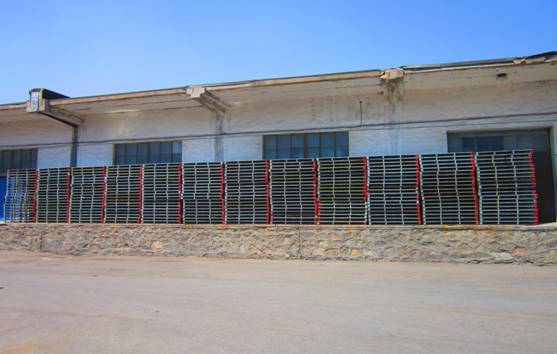
物流中心6号库站台
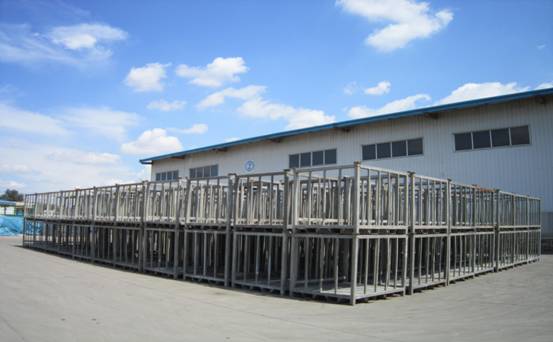
物流中心U型库场地
报道员:李鼎
|